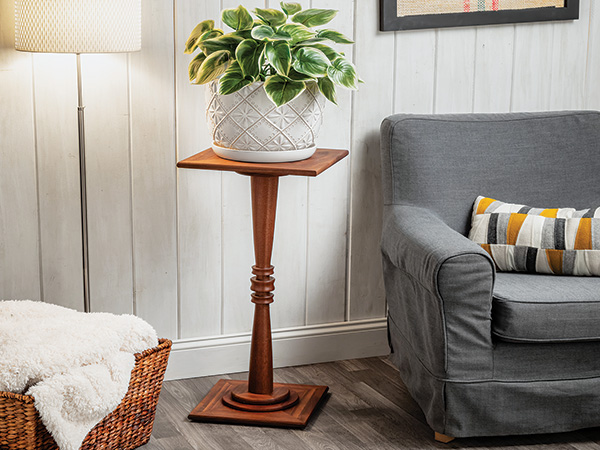
We’ve had this old-fashioned candy machine in our family for some time, and while I have been meaning to make a nice stand for it, other projects and commitments seemed to always get in the way. But recently I acquired a Rockler VS 12-24 Variable Speed Midi Lathe with the accessory bed extension, and I knew I had the perfect project for this lathe!
The candy machine fits well on the smaller top specified in the Material List But you might prefer to make the larger top instead and use this Pedestal Stand to display a big house plant or other object. Either way, let’s get started making it!
Milling and Gluing
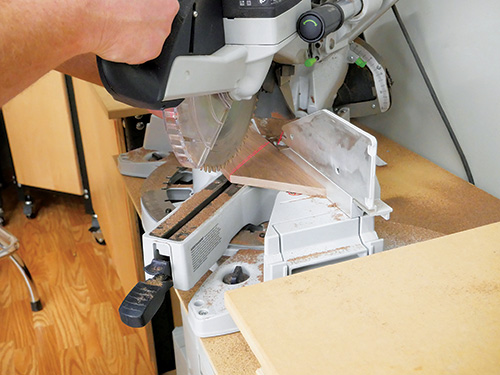
Notice in the Exploded View Drawing that while the small top is an edge-glued panel, the stand’s discs, base and large top are each made up of four sections miter-cut into 45°-45°- 90° triangles that are glued together into blanks to hide the end grain.
I settled on walnut for my project. At the table saw, I started by ripping enough of it and crosscutting it into sections (outlined in the Material List) to make each of the discs and the stand’s base. The two 6″ discs need material ripped to 3″ wide; the 7″ disc needs 3-1/2″-wide stock and the 8″ disc requires 4″-wide stock. Do the same for the stand’s base sections and the larger top, if that’s the top you’ve chosen for your project.
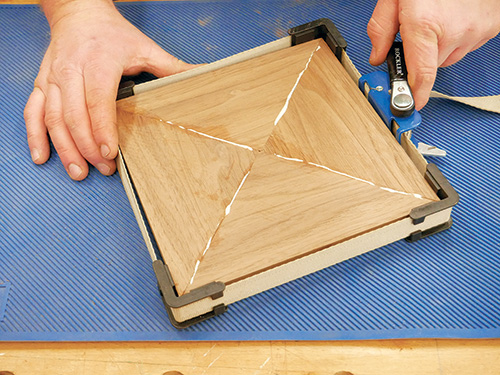
From here, I took all the sections to my miter saw, swiveled it to exactly 45 degrees and miter-cut each section into a triangle. Keep in mind that the “top” of each triangle should be oriented at the edge of the workpiece and centered on the section’s length. The tops of the triangles form a square corner. You may want to test your saw setup on scrap wood first to make sure four triangles will fit together without creating gaps.
Once all those are cut, it’s time to glue together blanks for the discs and base (and large top, if you’re making one). A strap clamp is ideal for this job. Apply a liberal amount of glue to all joints before assembling each group of four triangles, and make sure you don’t overtighten the clamp that co uld push the joints out of alignment! When the blanks dry, scrape off any glue and sand their faces flat. My random orbit sander with 80-grit sandpaper made quick work of that task.
Routing Round Discs
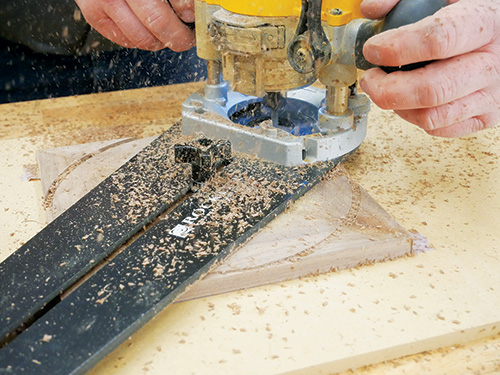
I used Rockler’s Circle Cutting Jig for Compact Routers to turn my square blanks into four discs. To use this jig, first drill a 9/32″ center hole to register the jig’s pivot pin and then set it for each disc’s radius. With a 1/4″ straight bit installed and my compact router mounted on the jig, three progressively deeper passes in a clockwise direction cut through the stock. Secure each disc blank temporarily to a sacrificial board before routing it round. Next, I eased the top and bottom edges of the discs, as well as the flat edges of the base, with a 3/8″ roundover bit. Sand these parts up through the grits to 220 and apply a finish of your choice. I chose hard wax oil.
Off to the Lathe!
![]() |
![]() |
It’s time to turn the pedestal! Start by cutting yours to length, marking the centers of the ends and dimpling those centers with an awl. Mount it on the lathe. I reached for a spindle roughing- out gouge to turn the pedestal blank into a cylinder. Take care to maintain a consistent diameter. Then, I referenced the Pedestal Detail Drawing and used a caliper and parting tool to establish final diameters at all of the key locations on the workpiece.
![]() |
![]() |
Check your sizing periodically with a caliper. |
Turn the long tapered areas of the pedestal to shape using a spindle roughing-out gouge or a skew chisel. Try to keep the tapers as flat as possible |
From there, I used various traditional and carbide-insert lathe tools to turn the pedestal to final shape. While tapering the long top and bottom “straight” areas of the spindle, I found it helpful to reference against a long rule to identify any high or low spots that needed attention. Make these tapers as straight as you can.
![]() |
![]() |
A long rule will reveal any high or low spots of your taper cuts. |
Here, a spindle gouge shapes a concave recess into the center of each of the spindle’s three middle rings. A round carbide-insert tool is another good option for this shaping step. |
The narrow center “ring” details have a slight undercut on each of their top and bottom faces. This creates the illusion that they’re floating. A diamond-shaped carbide-insert tool excelled at reaching into these tight places for me.
![]() |
![]() |
The author found a diamond-shaped carbide-insert tool helpful for working inside of the narrow areas between the rings when forming their slight top and bottom undercuts. |
Hard wax oil or a shellac-based friction polish applied on the lathe are two quick finish options for this project’s pedestal. Or wait until after final assembly and spray it with an aerosol finish instead. |
When the turning is done, sand the pedestal up to 220-grit and apply finish while it’s still mounted on the lathe. If you’re making the small top for this project, glue up a blank for it, cut it to final shape and sand and finish it. I rounded the corners of mine to 1-1/4″ radii at the bandsaw.
Putting the Pieces Together
![]() |
![]() |
Install rubber feet on the base, then attach the base and bottom discs to the pedestal with a 4″ lag screw. Counterbore the screwhead. |
Install the top two discs on the pedestal with another 4″ lag screw, just as you did for the base and bottom discs. |
That brings us to final assembly. I attached screw-on rubber feet to the base to protect the floor and create a shadow line there. Now use two #14 x 4″ lag screws to attach each stack of discs and the base to the pedestal. Be sure to first drill a pilot hole and a counterbore to recess the lag screw heads before driving the fasteners home. I grabbed several long #8 wood screws to attach the base of the candy machine and the top panel to the top disc.
![]() |
![]() |
The author mounted the candy machine’s metal base and top panel to the stand’s top disc by driving #8 x 1″ screws down through the parts. |
If the top surface of your pedestal stand’s top will be visible, drive #8 x 1-1/2” screws through the upper discs from below to install it in order to hide the screwheads. |
Once that was done, I could finally check this project off the to-do list! Now we’ve got a proper wooden stand for our family’s candy machine, and my new benchtop lathe tackled its first big turning job with flying colors!